Some years ago I bought a set of MCL highway blades from another member here. After using them on a multi-day, 1,600 mile trip it was apparent that they were not going to do the job for me, so I re-sold them to another member.
Earlier this year, after the apparent demise of MCL as a going concern, and with unmet demand for highway blades evident, a new vendor stepped in to fill the void. That is PSR. They floated the concept, showing photos of 3D-printed prototypes and asking whether there would be sufficient interest here to merit a production run. I gave them my feedback and opinion on the MCL version, including a discussion of why they weren't for me. PSR listened and responded accordingly. Their blades are longer than the MCLs, mount differently (about which a bit more, below), and feature a different overall shape to the foot rest.
Taking advantage of the limited-time pre-production pricing offer, I rolled the dice and ordered a set. PSR was very good about posting progress updates to the forum, and shipped the finished product a month ahead of the originally- announced schedule.
Whenever I get a new product like this I like to take an inventory of what's in the box, and work out how it all goes together. There are no instructions provided with this product, so it fell to me to figure it out. Happily, there isn't a lot that isn't obvious. I also determined that the tools needed are 5, 6, and 8 mm hex keys and a 17 mm open-end or box-end wrench. A torque wrench will be handy for getting the mounting bolts well-secured and getting even tension on the pivot bolts.
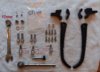
INSTALLATION PROCESS
These blades are pretty easy to install. Obviously the tip-over guard covers have to come off (the blades come with a template to use as a pattern if you choose to cut them for reinstallation after the blades are on, but I'm hedging my bets until I have decided whether the blades are "keepers" for me). After some hemming and hawing, I also found that I needed to remove the lower fairings, in order to have room to work a hand up and behind the tip-over guards themselves so that I could hold the backing plate in place while starting the bolts. Once the first bolt is started (it doesn't even have to be snug, just started) everything else follows pretty easily.
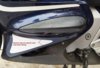
The blades mount onto the short section of straight tubing, ahead of the weld for the curved part of the tip-over guard and the bolt that secures the upper fairing to the guard. The outer part of the fixed mount even has chamfers that conveniently align with the rounded areas of the cutout in the fairing, where the tab for the plastic cover goes. This helps ensure that you have the blades mounted in exactly the same position from one side to the other.
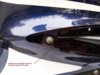
I found the easiest way to proceed was to first get a bolt inserted into one of the holes in the outer mount and get the 5 mm hex key inserted ahead of time. Next, I laid the curved back mounting plate on top of the mounting area and then rotated it to approximate final orientation with one hand while holding it with the other hand, lying on my side and reaching in from underneath. (NOTE: this is NOT a job to do when the exhaust system is hot... you WILL come in contact with the pipes.)
With one hand holding the backing plate in place, use your free hand to put the other part of the mount in position and start the first bolt to join the two pieces. After you've got it well started the assembly will stay put, freeing up both hands and letting you assume a more natural working position. Do not start snugging the bolts until you have them all well-started, to avoid accidentally cross threading them by having the axes of the holes not properly aligned.
Once you have everything started, go ahead and torque them down to "good and snug". (I didn't think to take my torque wrench out to set or measure how much I tightened anything; I just used the hex key. And in fact, for the upper bolts, the holes are deep enough that my hex key sockets cannot reach the bolts so I'd only be able to use the torque wrench on the lower bolts anyhow.) [EDIT: I took a guess, used the torque wrench, and torqued the lower bolts to 10 lb-ft, which was enough for the blades to not rotate on a follow-up static test.]
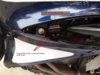
Once you have the mount firmly in position, put the spring into the hole on the upper side of the outer mounting piece, and carefully!! place the BB on top of it. TIP> lay a towel under the bike, being sure it extends far enough on both sides to prevent the BB from hitting the ground and bouncing WHEN (not if) you accidentally dislodge it. Also, double the towel over so that it is extra-deadening. I didn't do either of those things on the first side (photo below), and the BB ended up about 6 feet from the bike when I dislodged it. Took me ages to find it.
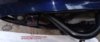
Next install the moving foot rest blade itself. It's easiest to do in its fully-deployed position. You won't be able to run the pivot bolt all the way through and get everything lined up ahead of time (or at least, I couldn't). Instead, CAREFULLY lower the blade so that you trap the BB and depress the spring slightly, then work the pivot bolt into position. A dab of lightweight grease between the movable blade and fixed mount couldn't hurt anything but doesn't seem strictly necessary.
Place the flat washer on the underside of the bolt and start the nylock nut. When you reach the nylock area, use your 8 mm hex key and 17 mm wrench to tighten the assembly to its final torque. The washers supplied will bend as you torque the pivot bolt and nut, to conform to the curve at the bottom of the fixed mounting block.
The blade should deploy freely under moderate pressure, and should not have any vertical play. You can hear the BB snap into the detent at full deployment; I don't *think* it quite reaches the detent at the fully-retracted position or at least I could not hear it click. You can easily check whether you have the blades tight enough to suit your taste, by operating them by hand. Adjust the torque on the pivot bolt accordingly.
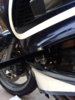
Finally, insert the 6 mm bolt through the provided aluminum spacer / sleeve and install into whichever hole you prefer, at the ends of the curved part of the blade.
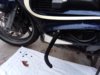
Repeat for the other side, reinstall the lower fairings (and modified tip-over guard covers if you elected to cut yours), put the bike on the center stand to give them a static test, and go ride!
FIRST IMPRESSION
This is a simple-to-install product that appears to be rugged and robust enough to provide years of service. My static sit-test proved that I do not have the mounting bolts tight enough, because the blades rotated under the weight of my feet and legs. That will be easy to fix, although in order to do the job properly I'll need to remove the blade arms to get access to the upper mounting bolts. At least I don't have to take the lower fairings off again.
Whether it's because I did the test in regular shoes rather than my riding boots, or because I have not reinstalled the plastic tip-over guard covers, or because the blades themselves are longer than their MCL predecessors, the PSRs don't spread me out the way the MCLs did, and don't seem to cause me to have my calves jammed up against the edge of the middle cowling. Now I need to go run with them for a few thousand miles, but that will be a project for next spring or summer since the bike is about to go into its annual winter exile at the storage facility.
Earlier this year, after the apparent demise of MCL as a going concern, and with unmet demand for highway blades evident, a new vendor stepped in to fill the void. That is PSR. They floated the concept, showing photos of 3D-printed prototypes and asking whether there would be sufficient interest here to merit a production run. I gave them my feedback and opinion on the MCL version, including a discussion of why they weren't for me. PSR listened and responded accordingly. Their blades are longer than the MCLs, mount differently (about which a bit more, below), and feature a different overall shape to the foot rest.
Taking advantage of the limited-time pre-production pricing offer, I rolled the dice and ordered a set. PSR was very good about posting progress updates to the forum, and shipped the finished product a month ahead of the originally- announced schedule.
Whenever I get a new product like this I like to take an inventory of what's in the box, and work out how it all goes together. There are no instructions provided with this product, so it fell to me to figure it out. Happily, there isn't a lot that isn't obvious. I also determined that the tools needed are 5, 6, and 8 mm hex keys and a 17 mm open-end or box-end wrench. A torque wrench will be handy for getting the mounting bolts well-secured and getting even tension on the pivot bolts.
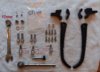
INSTALLATION PROCESS
These blades are pretty easy to install. Obviously the tip-over guard covers have to come off (the blades come with a template to use as a pattern if you choose to cut them for reinstallation after the blades are on, but I'm hedging my bets until I have decided whether the blades are "keepers" for me). After some hemming and hawing, I also found that I needed to remove the lower fairings, in order to have room to work a hand up and behind the tip-over guards themselves so that I could hold the backing plate in place while starting the bolts. Once the first bolt is started (it doesn't even have to be snug, just started) everything else follows pretty easily.
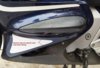
The blades mount onto the short section of straight tubing, ahead of the weld for the curved part of the tip-over guard and the bolt that secures the upper fairing to the guard. The outer part of the fixed mount even has chamfers that conveniently align with the rounded areas of the cutout in the fairing, where the tab for the plastic cover goes. This helps ensure that you have the blades mounted in exactly the same position from one side to the other.
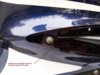
I found the easiest way to proceed was to first get a bolt inserted into one of the holes in the outer mount and get the 5 mm hex key inserted ahead of time. Next, I laid the curved back mounting plate on top of the mounting area and then rotated it to approximate final orientation with one hand while holding it with the other hand, lying on my side and reaching in from underneath. (NOTE: this is NOT a job to do when the exhaust system is hot... you WILL come in contact with the pipes.)
With one hand holding the backing plate in place, use your free hand to put the other part of the mount in position and start the first bolt to join the two pieces. After you've got it well started the assembly will stay put, freeing up both hands and letting you assume a more natural working position. Do not start snugging the bolts until you have them all well-started, to avoid accidentally cross threading them by having the axes of the holes not properly aligned.
Once you have everything started, go ahead and torque them down to "good and snug". (I didn't think to take my torque wrench out to set or measure how much I tightened anything; I just used the hex key. And in fact, for the upper bolts, the holes are deep enough that my hex key sockets cannot reach the bolts so I'd only be able to use the torque wrench on the lower bolts anyhow.) [EDIT: I took a guess, used the torque wrench, and torqued the lower bolts to 10 lb-ft, which was enough for the blades to not rotate on a follow-up static test.]
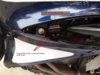
Once you have the mount firmly in position, put the spring into the hole on the upper side of the outer mounting piece, and carefully!! place the BB on top of it. TIP> lay a towel under the bike, being sure it extends far enough on both sides to prevent the BB from hitting the ground and bouncing WHEN (not if) you accidentally dislodge it. Also, double the towel over so that it is extra-deadening. I didn't do either of those things on the first side (photo below), and the BB ended up about 6 feet from the bike when I dislodged it. Took me ages to find it.
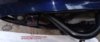
Next install the moving foot rest blade itself. It's easiest to do in its fully-deployed position. You won't be able to run the pivot bolt all the way through and get everything lined up ahead of time (or at least, I couldn't). Instead, CAREFULLY lower the blade so that you trap the BB and depress the spring slightly, then work the pivot bolt into position. A dab of lightweight grease between the movable blade and fixed mount couldn't hurt anything but doesn't seem strictly necessary.
Place the flat washer on the underside of the bolt and start the nylock nut. When you reach the nylock area, use your 8 mm hex key and 17 mm wrench to tighten the assembly to its final torque. The washers supplied will bend as you torque the pivot bolt and nut, to conform to the curve at the bottom of the fixed mounting block.
The blade should deploy freely under moderate pressure, and should not have any vertical play. You can hear the BB snap into the detent at full deployment; I don't *think* it quite reaches the detent at the fully-retracted position or at least I could not hear it click. You can easily check whether you have the blades tight enough to suit your taste, by operating them by hand. Adjust the torque on the pivot bolt accordingly.
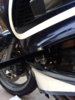
Finally, insert the 6 mm bolt through the provided aluminum spacer / sleeve and install into whichever hole you prefer, at the ends of the curved part of the blade.
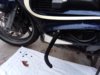
Repeat for the other side, reinstall the lower fairings (and modified tip-over guard covers if you elected to cut yours), put the bike on the center stand to give them a static test, and go ride!
FIRST IMPRESSION
This is a simple-to-install product that appears to be rugged and robust enough to provide years of service. My static sit-test proved that I do not have the mounting bolts tight enough, because the blades rotated under the weight of my feet and legs. That will be easy to fix, although in order to do the job properly I'll need to remove the blade arms to get access to the upper mounting bolts. At least I don't have to take the lower fairings off again.
Whether it's because I did the test in regular shoes rather than my riding boots, or because I have not reinstalled the plastic tip-over guard covers, or because the blades themselves are longer than their MCL predecessors, the PSRs don't spread me out the way the MCLs did, and don't seem to cause me to have my calves jammed up against the edge of the middle cowling. Now I need to go run with them for a few thousand miles, but that will be a project for next spring or summer since the bike is about to go into its annual winter exile at the storage facility.
Last edited: