This is assuming fork bushings aren’t worn. Straight fork tubes with worn bushings will show wobble.You could that without the dial indicators or anything. Remove the fork assembled, clamp the lower end down with C clamps or wood clamps to a solid work table along the table top not off the edge and rotate the tube in the lower. Watch for up and down on the little end as you rotate. If it is bent any it will move up off the table farther. if it is straight the tube will not go up or down.
String/straight-edge test won’t show that both fork tubes are bent straight backwards by 100mm on both sides in frontal impact because sides of tyres will still be parallel. Wheelbase will just have been shortened by 100mm.
Ultimately measuring individual pieces of fork assembly is sure way to determine how bent they are. V-block for tubes and dial indicator to measure actual run-out amount. Can bend back minor damage with C-clamp.
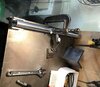
For larger amounts of damage on impossible-to-replace tubes, use sturdier arrangement.
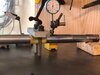
Due to high strength of these tubes, large amounts of bending needed to reverse damage.
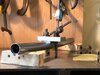
Once confirmed that both tubes are straight, they can be used as guides to gauge alignment of upper & lower triple-T clamps (without sliders). Better than that MotionPro tool is large piece of plate glass. About 30cm tall and wide enough to cover both fork tubes. Place it over tubes near bottom tips and verify that contact is even on both tubes. If triple clamps aren’t aligned, glass will wobble and only touch in 2 spots.
Last edited: